Behold The Hyundai Uni Wheel. Transportation May Never Be The Same
Behold The Hyundai Uni Wheel. Transportation May Never Be The Same
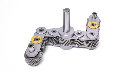
cleantechnica.com
Behold The Hyundai Uni Wheel. Transportation May Never Be The Same - CleanTechnica
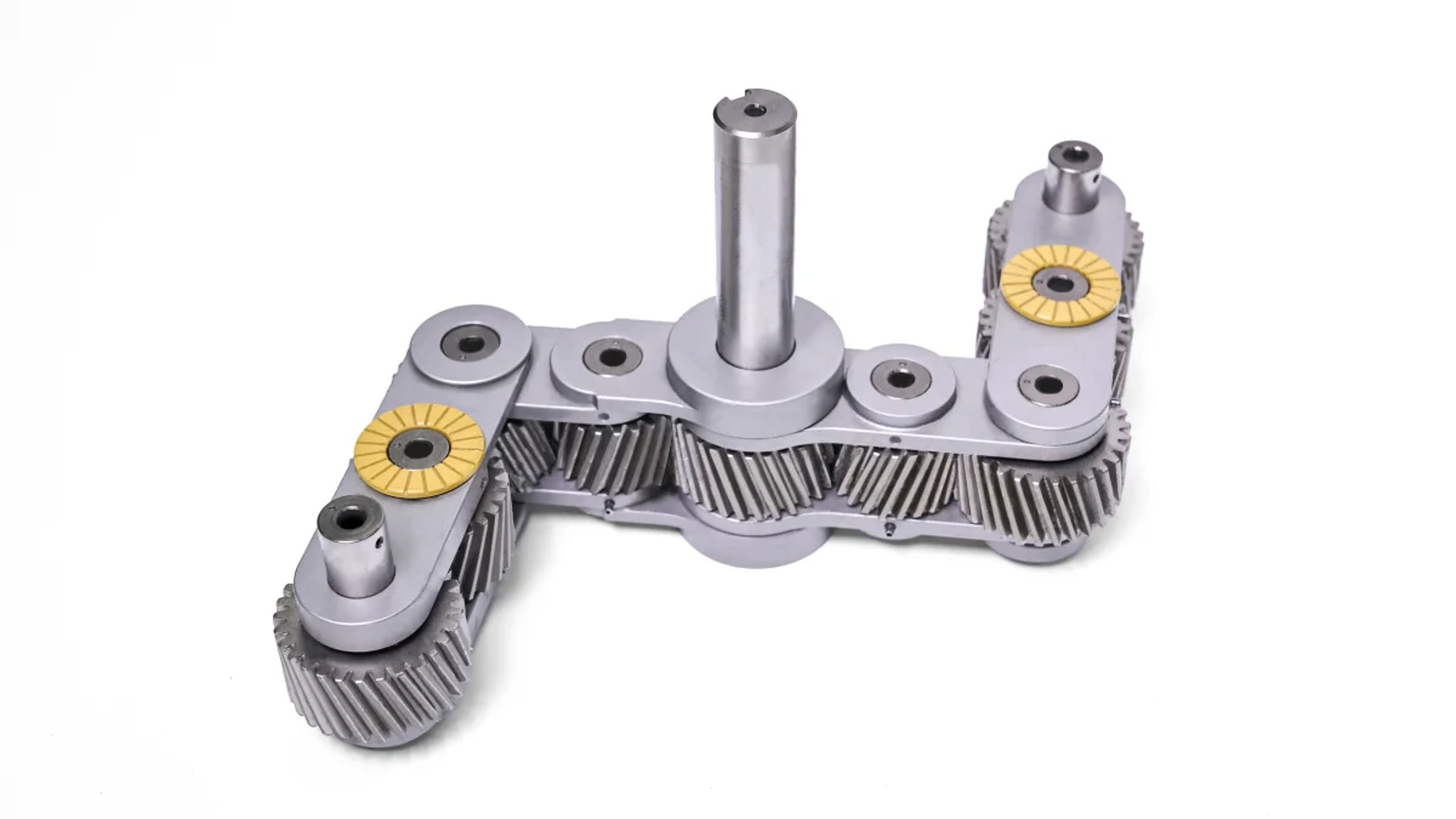
Behold The Hyundai Uni Wheel. Transportation May Never Be The Same
Behold The Hyundai Uni Wheel. Transportation May Never Be The Same - CleanTechnica